
Hi I’m Nathan
I am currently a senior Mechanical Engineering student at Cal Poly Pomona, a former Technician at Tesla, and a friend of Physics & Engineering.

LOX Chamber Thermal Analysis
Thermal Desktop Model
Developed a thermal model of a liquid oxygen (LOX) chamber to evaluate heat flow behavior in a lunar environment. The objective was to design a system that minimizes heat transfer to the LOX by introducing high thermal resistance paths, enabling passive thermal control. The model incorporated lunar surface conditions—such as vacuum, extreme temperature swings, and limited convective cooling
Reduced Order Model
Developed a reduced-order thermal model to efficiently simulate heat transfer across the system. Radiative heat transfer was modeled using radiation conductors, calculated with a ray count of 25,000 per node for improved accuracy. Conductive heat transfer was approximated based on fitting types, contact pressures, and metal-to-metal interfaces, following methodologies from the Spacecraft Thermal Control Handbook.
Thermal resistance values were derived using standard approximation techniques. The model considers only radiation and conduction as heat transfer mechanisms, with surface emissivities based on properties of polished metals.
Solar Flux Orbit Analysis
Developed transient thermal models to assess the impact of solar flux and lunar surface albedo on the LOX Chamber Lander while stationed on the lunar surface, accounting for its orientation and exposure to sunlight throughout the lunar day-night cycle. The model on the right shows the temperature of the LOX inside the chamber encasing, as it is maintained at roughly 90 Kelvin.
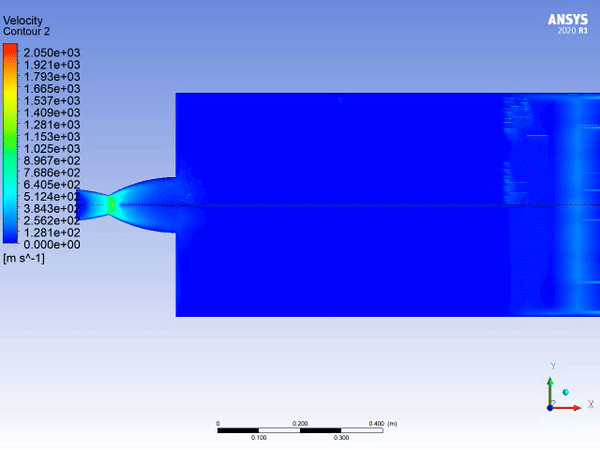
ANSYS Analysis on Rocket Engine CD Nozzle
ANSYS Mesh and Data Residuals
Meshed a two-dimensional view of an engine nozzle, and set boundary conditions for inlet, outlet, and symmetric axis to model fluid flow. Included scaled results for different properties of the fluid.
Fluid Temperature, Speed, Pressure
Performed a comprehensive analysis of the steady-state fluid dynamics within a rocket combustion chamber and nozzle using ANSYS Fluent. The analysis included the evaluation of key system properties; pressure, velocity, and temperature: presented in a combined contour plot, followed by individual contours depicting velocity, pressure, and temperature from left to right. This data facilitated the selection of optimal materials for the combustion chamber and nozzle, and enabled predictions regarding the exit flow characteristics.
Transient Heat Transfer Analysis
Transient heat transfer analysis on a model rocket nozzle using 3 different materials (Structural Steel, Copper, Inconel 718) to analyze heat transfer from the combustion chamber to the end of the nozzle.
Modal Analysis
Modal Analysis on two different materials to analyze the frequencies in which the greatest deflection occurs to predict its failure mode.
Transient - Mach Number

Rocket Structure - Nose cone : Recovery System
Proof of Concept - Prototype
Designed a recovery system for a model rocket that utilizes a servo motor, ultrasonic sensor, LCD, and springs to deploy a parachute at the rocket's peak altitude. The nose cone was engineered to split in half, incorporating hinges and locking pins that are released via the servo motor upon receiving a signal from the ultrasonic sensor. The sensor detects when there is an object placed within 10 cm, triggering a countdown displayed on the LCD. Two springs integrated into the structure ensure the cone halves open smoothly, allowing for reliable parachute deployment and safe recovery. The following structural parts were 3D printed; nose cone, structure, hinges, hinge connector, and locking pins.
Centrifugal Pump
Centrifugal Pump Model and Manufacturing
Developed a centrifugal pump and its encasing, carefully engineered for fluid movement. The pump will be powered by a 1000 RPM DC motor. In the upcoming phases, there are plans to conduct tests to assess the pump's performance.

Electromechanical Door
Design Objective
The goal for this proposal was to meet requirements for a space door that would be thermally resistant and soundproof. My main role was to select materials and the thickness for door design to withstand temperature and noise. Trade studies were done based off of density, thermal resistivity, and their sound dampening capabilities before selection of specific materials. The team decided to utilize Polyurethane spacers and Aerogel for our design.
Thermal Insulation
Hand calculated sound transmission loss and heat transfer through the door via conduction, radiation, and convection. Used ANSYS workbench computational fluid dynamics to analyze heat transfer on both sides of the door.

Prototype Mechanical Stairclimbing Assembly for Wheelchair
Model Stair Climber Assembly
Designed a conceptual stair-climbing attachment for wheelchairs using SolidWorks. The design incorporates linear actuators to pivot the mechanism into optimal positions for stair navigation. This concept will be further refined into a prototype for testing and proof-of-concept validation.
Design & Manufacturing
This is a prototype of an electromechanical stair climber assembly that will be able to attack to the bottom of a wheelchair and actuate the assembly for easy access. I modeled the prototype in Solidworks then printed the model using PLA for integration and testing.
Prototype
The prototype was assembled using standard fasteners, following its 3D printing process. The motors are controlled by Arduino microcontrollers interfaced with an L298 motor driver, allowing for direction reversal via programmed control. Communication between two separate Arduino boards is facilitated through Bluetooth transceivers, enabling the transmission of signals to alternate motor rotation directions.
Through four iterations of the design, minor adjustments were made to optimize the assembly's functionality. Each iteration focused on specific refinements, such as changing approach angle, improving alignment, adjusting weight balance, as well as redesigning the battery to output sufficient voltage for all motors.
Final Prototype and Proof of Concept
This is the final design for the prototype which included a less steep approach angle, weight balance adjustments by adjusting motor placement and driving wheels and finally adjusting output voltage and current to provide sufficient power to the motors.
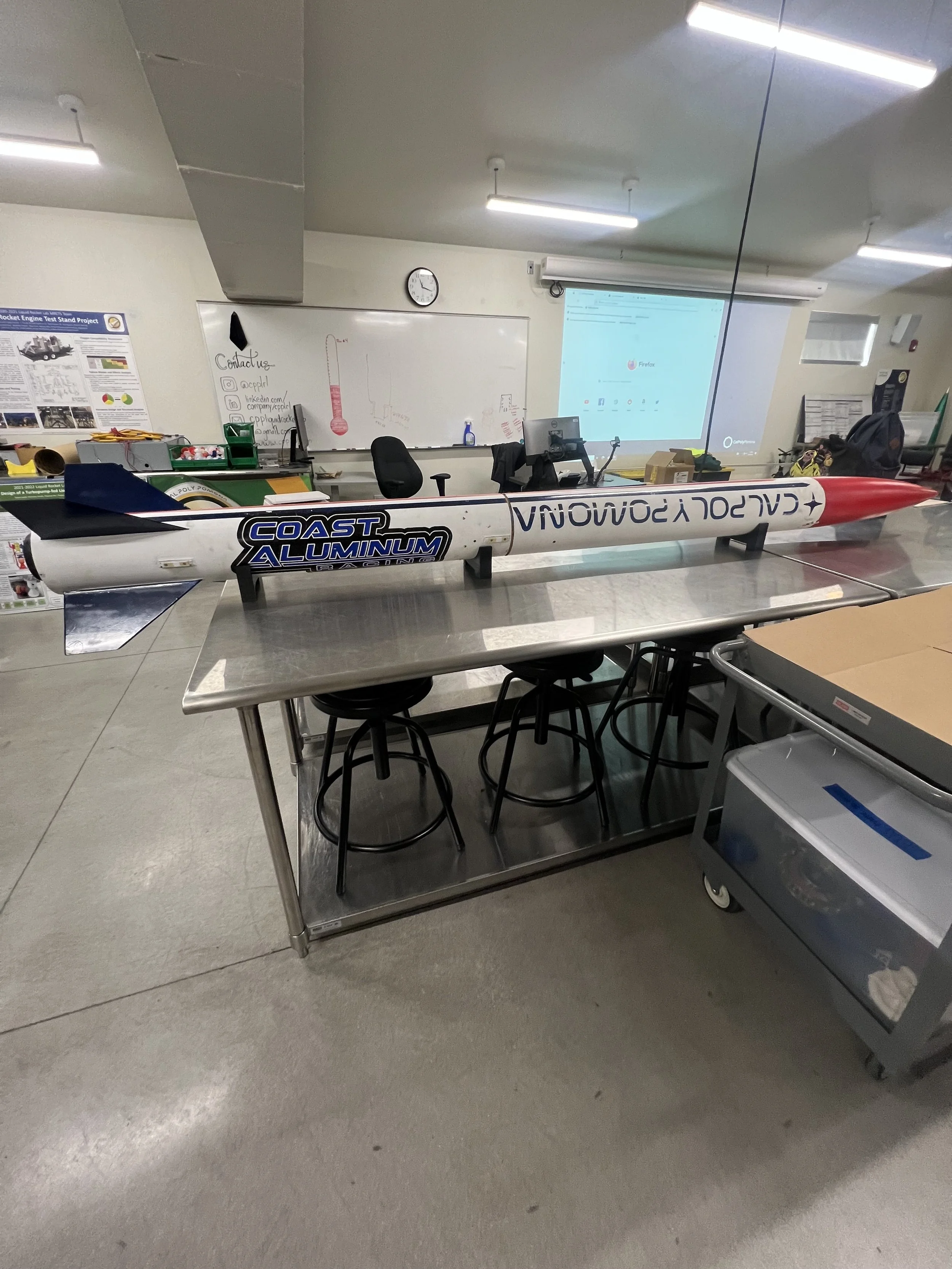
Instrumentation and Control for Liquid Rocket Engine
Actuators/Pressure Transducers/Thermocouples
Researched and down selected actuators based on torque requirements of the manual ball valves, which were hand tested in lab using a torque wrench. Tested pressure transducers/thermocouples for functionality to read atmospheric temperatures and pressures. These would eventually be integrated into the engine to analyze pressure and temperature readings in the propellent lines and main engine systems, ie. gas generator.
Fume Extractor
Fume Extractor
Designed and fabricated a fume extractor system utilizing a 3D-printed enclosure and a 12V DC motor to effectively remove fumes, preventing obstruction of view and minimizing inhalation risks.
Coming Soon
Modeling a 12U nanosatellite as a single rigid body to simulate rotational motion driven by a flywheel, followed by simulating solar panel rotations using ball gear mechanisms—all using quaternion-based dynamics